POLYESTER ROUNDSLING SAFETY BULLETIN
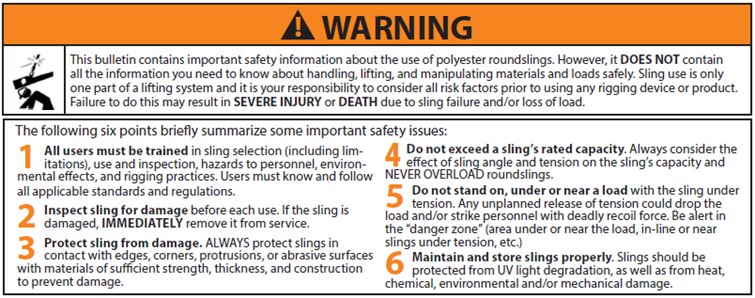
1. All Sling Users Must be Trained and Knowledgeable
All roundsling users must be trained on the proper use of roundslings. The American Society of Mechanical Engineers standard for sling safety (ASME B30.9) states:
“Synthetic roundsling users shall be trained in the selection, inspection, cautions to personnel, effects of the environment, and rigging practices as covered” by Chapter 9-6.
OSHA Guidance on Safe Sling Use (29 CFR 1910.184) states that a “qualified person” is one:
“who, by possession of a recognized degree or certificate of professional standing in an applicable field, or who, by extensive knowledge, training, and experience, has successfully demonstrated the ability to solve or resolve problems relating to the subject matter and work.”
It is important that all sling users be knowledgeable about the safe and proper use and application of slings and be thoroughly familiar with the manufacturer’s use and safety materials provided with each product. In addition, all sling users need to be aware of their responsibilities as outlined in all applicable standards (e.g., WSTDA RS-1 and RS-2; ASME B30) as well as all applicable provincial, state, federal, and OSHA regulations.
If you are unsure whether you have been properly trained, or if you are unsure of what the standards and regulations require of you, ask your employer for information and/or training—DO NOT use roundslings until you are absolutely sure of what you are doing. Remember, when it comes to using roundslings, lack of skill, knowledge and care can result in SEVERE INJURY or DEATH to you and others.
2. Slings Must Be Regularly and Properly Inspected
Even seemingly “minor” damage to a roundsling can significantly reduce its capacity to hold or lift objects and increases the chance that the sling will fail during use. Therefore, it is very important that roundslings are regularly and properly inspected. In reality, there simply is no such thing as “minor” damage. If you are not sure whether a sling is damaged, DO NOT USE IT.
2a. How to inspect slings
To detect possible damage, you should perform a visual inspection of the entire sling and also feel along its entire length, as some damage may be felt more than seen. You should look and feel for any of the types of conditions listed in Table 1. Table 2 shows examples of some of these types of damage, but note that they are relatively extreme examples provided for illustration purposes only.
2b. What to do if you identify damage in a sling
If you identify ANY of these types of damage in a sling, remove it from service immediately even if the damage you feel or see is not as extensive as shown in the pictures in Table 2. Slings that are removed from service must be destroyed and rendered completely unusable unless they can be repaired and proof-tested by the sling’s manufacturer or other qualified person. You should never ignore sling damage or attempt to perform temporary field repairs of damaged slings (e.g., tie knots in the sling, etc.).
2c. How often to inspect slings?
A three-stage procedure is recommended to help ensure that roundslings are inspected with appropriate frequency:
Initial Inspection—Whenever a sling is initially received, it must be inspected by a qualified person to help ensure that the correct sling has been received and is undamaged, and that the sling meets applicable requirements for its intended use.
Frequent Inspection—Slings must be inspected by the sling user before each use.
Periodic Inspection—Every sling must be inspected “periodically” by a qualified person. In order to validate the frequent level of inspection, the periodic inspection should be performed by someone other than the individual(s) that most commonly performs the frequent inspection. The frequency of periodic inspections is based on the sling’s actual or expected frequency of use, severity of service conditions, the nature of the work performed with the sling, and experience gained during the inspection of other slings used in similar circumstances. Periodic inspections intervals must not exceed one year. General guidelines for the frequency of periodic inspections are:
- Normal service—yearly
- Severe service—monthly to quarterly
- Special service—as recommended by a qualified person
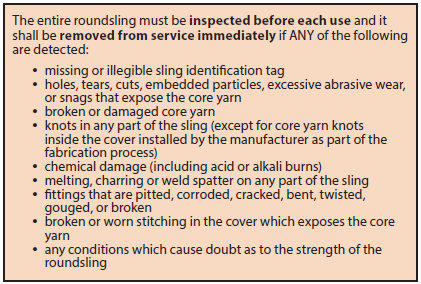
Written records documenting the condition of individual slings are not required for frequent inspections. WSTDA RS-1 and ASME B30.9 require that a written record be maintained documenting when the most recent periodic inspection was performed. If a sling has been idle or in storage for more than 1 year since the last periodic inspection, prior to use the sling must be thoroughly inspected by a qualified person per the requirements for periodic inspection – maintain documentation that this inspection was performed. See WSTDA RS-1 for more information about definitions of Normal, Severe, and Special service conditions.
3. Slings Must be Adequately Protected from Damage
3a. Avoid actions that cause damage to slings
You should always avoid any action that causes the types of damage identified in Sect. 2 of this Bulletin, including (but not limited to):
- dropping or dragging slings on the ground, floor or over abrasive surfaces
- pulling slings from under loads when the load is resting on the sling—place blocks under load if feasible
- shortening or adjusting slings using methods not approved by the sling manufacturer or qualified person
- twisting, kinking, or knotting the sling
- exposing slings to damaging chemicals
- exposing slings to sources of heat damage or weld spatter
- using slings or allowing exposure to temperatures above 194°F (90°C) or below -40°F (-40°C)
- “tip loading” a sling on a hook instead of centering it in the base or “bowl” of the hook
- using hooks, shackles or other hardware that have edges or surfaces that could damage sling
- running/driving over slings with a vehicle or other equipment
You also need to select and use proper connection hardware with roundslings to avoid damage (see Tables 4 and 5).
Synthetic slings are affected by some chemicals ranging from little to total degradation. Time, temperature and concentration factors affect the degradation. For specific applications, consult the manufacturer.
3b. Safeguard slings with sufficient protection
Synthetic roundslings can be damaged, abraded or cut as tension and compression between the sling, the connection points and the load develops. Surfaces in contact with the sling do not have to be very abrasive or have “razor” sharp edges in order to create the conditions for sling failure. Therefore, roundslings must ALWAYS be protected from being cut or damaged by corners, edges, protrusions or abrasive surfaces with protection sufficient for the intended purpose.
Abrasion protection will not prevent damage from cutting. If protection against cutting is necessary, use only sling protection that has been designed, tested, and rated by the manufacturer. There are a variety of types of ways to protect slings from damage. A qualified person might select and use appropriate engineered sling protection (e.g., sleeves, pads, corner protectors, etc.) specifically designed to protect slings from damage. Regardless of the method chosen:
- The goal is to ensure that the sling maintains its ability to securely lift the load while avoiding contact with damaging or abrasive surfaces under load.
- A qualified person must ensure that the protection method chosen is appropriate for the types of damage to which the slings will be exposed.
The protection used must not be makeshift (i.e., selecting and using cardboard, work gloves, or other such items based solely on convenience or availability).
Several “test” lifts, done in a non-consequence setting, may be necessary to determine the suitability of the protection device(s). After each “test” lift, the protection device(s) and sling(s) need to be inspected for damage and suitability.
You should keep in mind that no protection is “cut proof” and you should always operate within the specified limits of the sling and its accessories (e.g., hardware, sling protection, etc.). Roundslings must always be protected from coming into direct contact with any edges unless the contacting edges meet both of the following criteria:
- The edges must be smooth and well-rounded. Edges that are chamfered or flattened at an angle do not meet this criterion.
- The size of the edge radii must be adequately large. Table 3 shows the minimum edge radii suitable for contact with unprotected polyester roundslings.
One way to measure an edge radius is to measure the distance between the leading edge of the radius that is being measured (Point A) and the point where the radius initiates from the bottom edge of the surface (Point B) (see Figure 1).
In order to protect the roundsling, it is also necessary to select and use proper connection hardware. Connection hardware should be selected such that it either:
- conforms to the size requirements listed in Table 4 (choker and vertical hitches) or Table 5 (basket hitch)
- the bearing stress value at the connection does not exceed 7,000 lbs./in2 during sling loading (see WSTDA RS-1, Section 4.7 for the procedure for calculating bearing stress)
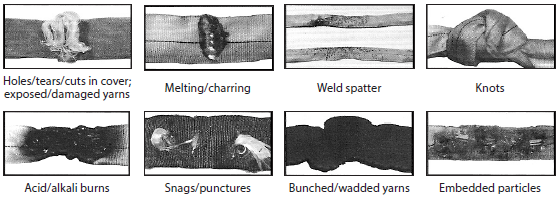
4. Always Use Slings Properly
When handling loads, a trained, qualified and knowledgeable user must take into account all risk factors and issues addressed in this bulletin, as well as considering any other relevant factors that may be appropriate. For roundslings, users must perform several activities, including (but not limited to) those discussed in the following subsections. Table 6 provides some, but not all, the factors that must be considered for successful load handling – also refer to ASME P30, ASME B30.9, WSTDA RS-1 and RS-2 for additional information.
4a. Assess the load
Determine the weight of the load (and, if more than one sling is used, the share of the load on each sling) and make sure it does not exceed the rated capacity of any sling or any of the components of the rigging system. Users must also determine the load’s center of gravity (CG) to make sure the rigging system used will be able to retain and control the load once lifted.
When multiple slings and/or multiple leg bridles are used with non-symmetrical loads, an analysis by a qualified person should be done to prevent overloading of any sling and/or leg.
4b. Select an appropriate sling/configuration
Select a sling having suitable characteristics for the type, size, and weight of the load, the share of the load, the type of hitch (see Table 7), and the environment. The sling must be securely attached to the load and rigged in a manner to provide for load control to prevent slipping, sliding, and/or loss of the load. A trained, qualified, and knowledgeable user must determine the most appropriate method of rigging to help ensure a safe lift and control of the load.
Another important consideration is the sling-to-load angle—the angle between a horizontal line and the sling leg or body. This angle is very important and can have a dramatic effect on the rated capacity of the sling. When the sling-to-load angle deviates from 90°, the tension on each leg increases.
This principle applies in a number of conditions, including when one sling is used to lift at an angle and when a basket hitch or multi-legged bridle sling is used. Table 8 provides information about increased tension as a function of sling-to-load angle (assuming equally-loaded sling legs). Sling angles of less than 30 degrees are not recommended.
Similarly, when the angle of choke is less than 120 degrees, the sling choker hitch capacity decreases. To determine the actual sling capacity at a given angle of choke, multiply the sling capacity rating (for a choker hitch) by the appropriate reduction factor determined from Table 9.
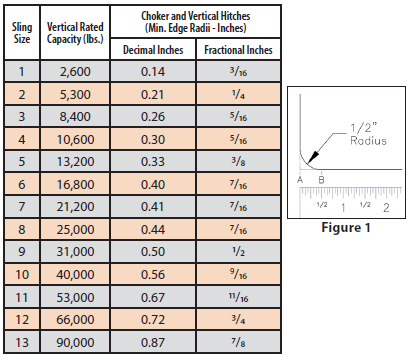
The radii values apply to roundslings that are fully tensioned to their rated capacity. When roundslings are tensioned to lower force values, the minimum radius values will reduce accordingly. Fractional inches are rounded up to the nearest 1/16”. For more information, refer to WSTDA RS‑1, Appendix 1: THE USE OF ROUNDSLINGS AROUND EDGES – Calculation Method.
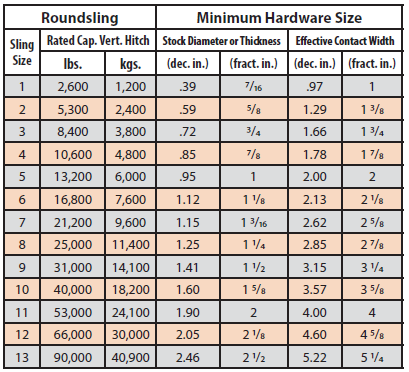
4c. NEVER shock load or misuse slings and rigging
NEVER shock load the sling or the rigging (i.e., accelerate/decelerate the load too quickly). Working load limits are based on moderately dynamic lifting or load-handling activities. Instantaneous changes (rapid acceleration or sudden stops) constitute hazardous shock loading which may overload the sling leading to sling failure, the unplanned release of tension and/or loss of load control. SEVERE INJURY or DEATH and/or property damage are potential outcomes of shock loading. NEVER misuse slings and rigging:
- NEVER pull on stuck, snagged, or restrained objects (load-measuring devices/methods must be used to ensure overloading never occurs).
- NEVER use slings for towing purposes.
A roundsling should only be used for load handling.
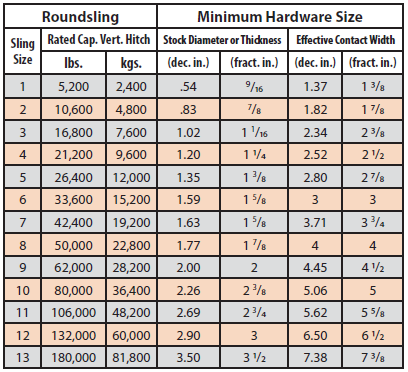
Table 5. Suitable connection hardware sizes for roundslings when used in a basket hitch.
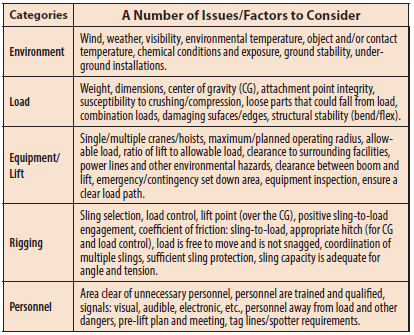
5. Make Sure All Personnel are Clear of Loads and Alert to Risks, Especially in the “Danger Zone”
Even if you account for all of the factors/issues discussed in this Safety Bulletin, things can still go wrong. Therefore, all personnel must be alert to potential risks associated with the use of roundslings, especially in the “Danger Zone.” The “Danger Zone” is any area where (a) the load could fall on or swing into personnel or property, or (b) deadly recoil could be produced by an unplanned release of tension. Therefore:
- All personnel must stand clear of lifted loads and never be under, on, or near suspended loads.
- Personnel must not stand in-line with or next to rigging under tension. Any unplanned release of tension could strike personnel with deadly recoil force.
- Personnel must be alert to the potential for the sling and/or load to become snagged/hung-up during load handling.
- Once load-handling activities begin, sling users must NEVER place any part of the body between the sling and the load or between the sling and hook/shackle/connection point and/or load-handling device.
- Personnel must never ride the sling or load.
NEVER ON. NEVER UNDER. NEVER IN-LINE.
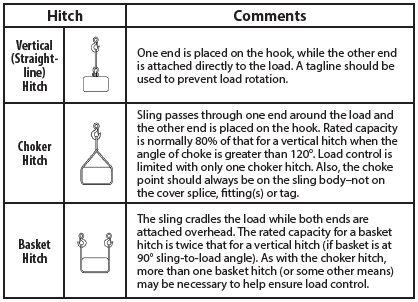
6. Properly Maintain and Store Slings
Slings should be protected from UV light degradation, as well as from heat, chemical, environmental and/or mechanical damage. In order to prevent damage to slings, especially when not in use:
- Store slings in a cool, dry and dark location to protect against UV light degradation and heat damage.
- Store slings in an area free from environmental, chemical, or mechanical sources of damage (e.g., weld spatter, splinters from grinding or machining, heat sources, etc.).
Do not scrub or wash roundslings, as a loss of strength is possible due to mechanical/chemical damage. Wet slings should be allowed to dry before being stored.
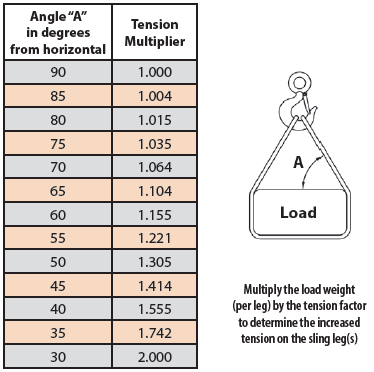
Table 8. Reductions in rated capacity as a function of sling – to – load angle
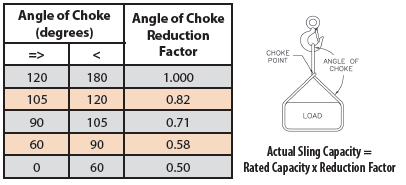